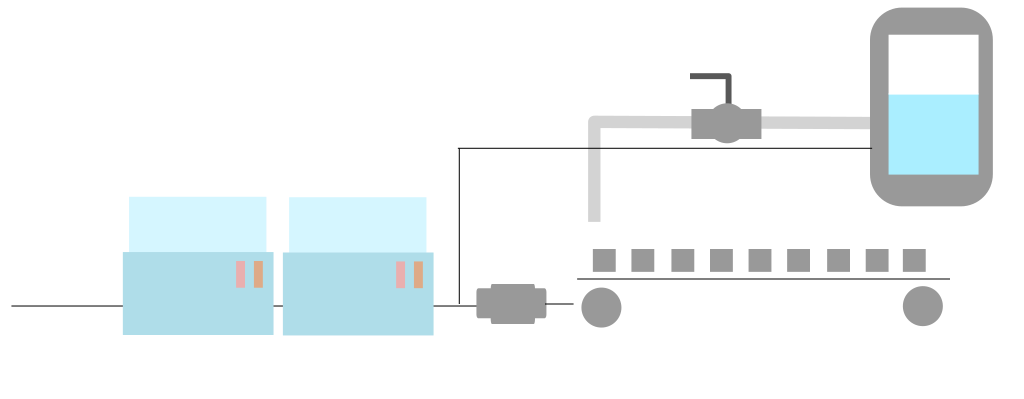
How did it come about
PLCs were created by General Motors in the 1960s. Prior to this the world was undergoing a major revolution where ICs were widely explored and evolved. But industrial automation still used its large relay panels. Although the best solution for the time was difficult to maintain, slow and their projects took a long time to complete.
What does it mean?
PLC stands for Programmable Logic Controller. It is commonly used in the industrial automation. These came to replace relay panels and to control sensors and actuators through pre-defined programming.
How do they work?
These handsets consist basically of three parts:
- Inputs – Where the controller senses the environment through sensors
- Processor – where the application programming schedules are executed
- Outputs – Sending commands to actuator devices according to the programming code.
One allusion we can make to controllers is the human body itself. Our five senses are the sensors (inputs) that send information to the brain (processor) that may or may not act on schedule. And our body as a whole will act according to the commands given by the brain. So we have a perfect example of how a controller works.
Both inputs and outputs can be information in two ways: digital or analog. Keeping this in mind we can say that the digital inputs are Yes / No, or in computer language, 0 or 1. This type of information can be used for when a button has been pressed or if a valve is on or off, for example. The analog type can bring different values, such as a thermometer that needs to bring the temperature or water volume of a certain container. This information can be sent to the processor for some decision making or also set by the output depending on the programming code. The programming is often coded through a type of software called “ladder”.
Of course, PLCs do not work alone, and besides sensors and actuators they need a main component to orchestrate the entire application, which is the SCADA system . For this the SCADA system must be prepared to communicate with each controller and have their drivers to communicate.
Main advantages
As I mentioned earlier, PLCs came to replace the large relay panels that existed in industries in the 1960s. But to better understand the firepower of these small devices, let’s list some of the many advantages they provided when they hit the market:
- easy maintenance
- drastic reduction of electrical panels
- provided faster projects
- reduction in energy consumption
- faster processing
- provided more complex mathematical operations
- communication with other devices
- higher reliability, fewer errors
- easy error / problem diagnosis
- among many others
Some sensors
Let’s bring here some examples of sensors and bring this theory to practice:
- button
- inductive sensor – detects metallic materials
- capacitive sensor – detects virtually any material nearby
- thermocouple – temperature
- optical sensor – detects when a beam of light is cut
Some actuators
Tires
Cylinders, Valves or Solenoids
Hydraulic
Cylinders, engine, pumps or presses
Electric
Motor, servo motor, electric lock or electric cylinder
Some examples of PLC manufacturers
- Schneider Electric
- Siemens
- Rockwell Automation
- Delta
- Weg
- Omron
- ABB
- Advantech
- Fatec
- Festo
- Koyo
- Mitsubishi
- Panasonic
- Phoenix
- Crouzet
- Unitronics
- Wago
- GE