SCADA
system PLC industry.
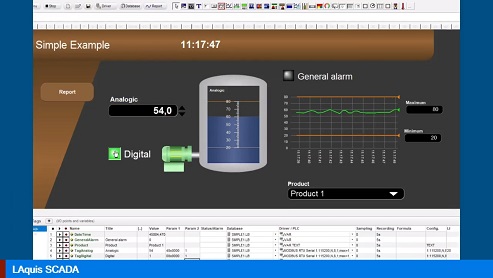
SCADA system
means supervisory control and data
acquisition system.
Its purpose is to control automation in industry gathering information from equipment like
PLC communicating
with a computer with SCADA software in real-time.
Work as HMI
(Human Machine Interface) in a computer.
Uses the SCADA database to store the data acquisition.
SCADA
system supervisory:
The SCADA system begins with a supervisory concept in the field of the ICS (Industrial Control System). Management of
industry data is important to an administration control system. Data
acquisition from equipment like PLC (programmable logic controller) in real-time and organized reports improves
company management solutions. Solutions like this, allied to industrial
automation, result in quality improvements.
PLC is a Programmable Logic Controller. It is a hardware that can be
used to control processes in a factory plan.
Its information can be passed to the PLC SCADA systems in a computer.
The SCADA can monitor in real-time, control, record, and generate
reports from this information.
In a supervisory, the SCADA systems organize that information from the
industrial factory through communication with PLC and data acquisition equipment.
The information goes from users in a factory to general
management.
The SCADA systems can monitor the industrial information through HMI
panels in screens and reports with data from the recorded database.
The data acquisition can be stored in databases and distributed as
needed.
SCADA panels can be replicated in the network via LAN / WEB. Several
users are able to monitor the SCADA system supervisory.
The screen can be customized according to each case.
HMI objects are distributed in monitor creating control panels and
plant schemes.
Animated objects pictures with graphic information are used to improve
SCADA supervisory.
These objects can be displays, controls, bar graphs, gauges, valves,
pumps, buttons, charts, etc.
SCADA control system with supervisory:
They can interact with SCADA users by clicking and typing.
When these objects are used, information can be sent to PLC to control
data acquisition in the factory.
SCADA data is passed to them. Users are able to get SCADA information
through this.
The PLC SCADA can control the supervisory information through users and
programming applications.
Scripts can be used for programming an application.
Automate systems getting input information, calculating, and generating
output data to the factory.
SCADA programming:
The SCADA systems are programmable according to each supervisory case.
If some data are included in some condition then information is sent
to the PLC equipment.
And logical conditions define SCADA systems way to proceed with the specific
applications.
This programming can be made via script in SCADA.
The SCADA systems control automation in the factory.
Scripts are commands in several languages depending on the platform.
These commands can send and receive data to the SCADA system according
to each application case.
PLC SCADA:
Data acquisition that came from PLC is made through networks like
Ethernet and serial. Each PLC has protocols defined over these
supervisory networks.
For example, Ethernet can be used with MODBUS TCP protocol.
There are several PLC with communication that can be used in SCADA
automation.
These PLC can be distributed in a factory and connected.
The SCADA systems can centralize supervisory information of all PLC in
a net.
SCADA database:
SCADA system data are recorded in a SCADA database. This database can be
SCADA proprietary or ODBC base. The SCADA software has these options.
Databases are tables of values that are used to store information about
the system.
Each table has fields. Each field can be a SCADA tag from PLC or variable.
Database fields may store values in number or text format according to
the case.
Each register is a set of fields recorded.
Each scanning value is a register.
Inside this register, it can be stored a time field and header
information before the values from data acquisition.
Auxiliary tables of products, recipes, customers, etc... can be used in
the SCADA system to improve.
PLC data acquisition passed to supervisory SCADA can be stored in this
database.
SCADA reporting system:
After data stored in the database, reports can be generated.
Listing of the SCADA system tag fields. They can be formatted according
to each case.
Several reports of PLC SCADA data acquisition are created for the
manager.
Alarms can be set to trigger events. Limits maximum and minimum for
each tag case.
Calculation according to process.
These SCADA system alarms are stored and recognized. Can be set in real
time.
When data acquisition values reach alarm limits an event can be
triggered.
The alarm is stored and informed to the SCADA system.
Measuring Instrument:
The measurement of length, velocity, weight, pressure or temperature values are performed by measuring instruments and equipment. Sensors can acquire units in meters, centimeter, mm, m/s², bar, °C units, etc.
Tools that have serial communication are used for data acquisition.
Equipment is sometimes placed on an electronic instrument cluster. Instruments used can also be flowmeters, pH meter, angle measurement equipment, velocity, etc.
the quality of the measurements is important in relation to the reference. Therefore, a calibration calculator is necessary in the area of metrology.
Through an uncertainty calculator, calibration can be performed to compare the values.
Another detail, is the calibration certificate, a calculator of measurement uncertainty.
Security:
Another important issue is security.
The software should have some options to help with security.
For example, remote applications must be
secured from non-authorized external controls.
SCADA industrial solutions examples introduction:
There are several control fields in the industry. Metal, manufacturing,
electric, food, chemical, automobile, etc...
Temperature SCADA system:
SCADA information of temperature can be monitored. Low, average, or high
temperatures are stored to assure process quality.
Limits and alarms are set to quality assurance.
If some temperature reaches limits, an occurrence is triggered for
action and explanation in the report system.
When SCADA recipes are set, the SCADA system must control from start to
finish of each process in the factory.
In temperature control, a setpoint must be defined for each case.
Microcontrollers can be used to set data PID in the industry.
Pressure SCADA system.
SCADA information of pressure can be monitored. Limits and alarms are
set to quality assurance.
If some pressure reaches limits, an occurrence is triggered for action
and explanation in the report system.
When SCADA recipes are set, the SCADA system must control from start to
finish of each process in the factory company.
SCADA production counting.
SCADA system can do the counting of products on a production
line. Each product that passes to the sensor sends to PLC a
signal. A counter is used as a tag in SCADA to increase the value to the
number of items. These items can be products, objects, events, users,
etc...
SCADA water treatment
In the SCADA system, each step of water treatment can be supervised and
controlled. Levels, pressures, temperatures, events, alarms, etc...
Pumps can be monitored and triggered when needed. Valves also are
controlled by SCADA.
Each variable can be reported in SCADA that was recorded in the
database.
Sistema SCADA
SCADA Sistemi
SCADA Software
|